Are you eager to improve the performance and productivity of your commercial laundry equipment?
If the idea of reducing operational setbacks, boosting efficiency, and optimizing overall productivity interests you, you’re in the right place. Discover how adopting a connected laundry system, powered by Internet of Things (IoT) technology, can completely change your laundry operation.
In this article, we’ll explore nine benefits that come with integrating IoT-enabled connected laundry systems, offering you the key to heightened facility safety, unparalleled efficiency, and enhanced productivity in your laundry operations.
What is a Connected Laundry System?
Connected laundry systems leverage advanced data analytics to provide a holistic understanding of operations, dosing, compliance, and machine performance. Washing machine operators can gather crucial data, including temperature, water flow, load weight, cycle times, and current operating status.
This real-time information empowers operators to assess performance on the fly, make necessary adjustments, and predict potential machine failures.
Through an IoT enabled virtual dashboard users gain complete visibility of the collected data. The information is presented through easy-to-interpret key performance indicators, providing valuable real-time insights into operations. This in-depth understanding not only allows for continuous improvement in operational efficiency, but also contributes to lowering the overall cost of cleaning. Additionally, the system enables the scheduling of routine maintenance based on actual wear and tear, emphasizing a proactive approach.
Together, these features enhance laundry management, offering efficiency, predictive maintenance, and cost-effective solutions.
How Do Connected Laundry Systems Work?
The IoT is a framework that involves connecting everyday devices to the internet, enabling them to send and receive data. This network of devices, equipped with sensors and communication capabilities, forms a smart system that can collect, exchange, and use data for various purposes
In the laundry industry, IoT revolutionizes traditional processes by incorporating smart technologies into washing machines, dispensers, and other equipment. Connected laundry systems utilize IoT to gather data on machine performance, water usage, chemical dispensing, and more.
This data is then transmitted in real time, allowing operators or technicians to monitor and control laundry operations remotely via a virtual dashboard. For example, in the context of smart laundry dispensers, IoT ensures precise chemical dilution, minimizing waste and optimizing cleaning outcomes.
The result is an interconnected and data-driven laundry ecosystem that enhances efficiency, reduces costs, and enables predictive maintenance.
Connected laundry systems feature two main components:
- Smart Dispensers
- Virtual Dasboard
Smart Laundry Dispensers
A smart laundry dispenser is a chemical dispensing unit that can be precisely programmed to function without the need for constant human supervision. Remarkably, a technician can preconfigure the smart laundry dispenser remotely without ever needing to set foot on your facility’s premises, after installation, of course.
What makes a smart laundry dispenser ‘smart’ is that it can connect to other devices via IoT and has the capability to dispense a predetermined amount of chemicals at specific intervals during the wash cycle. In doing this, the smart laundry dispenser eliminates the uncertainty surrounding how much detergent is needed for each laundry load.
Incredibly, any commercial laundry machine can be retrofitted to be included in the connected laundry system. You can connect multiple machines to one smart laundry dispenser and begin monitoring each one on the virtual dashboard. Using multiple smart laundry dispensers, you can connect any number of machines across multiple buildings, all monitored on the same virtual dashboard.
Virtual Dashboard
When using a connected laundry system, you are given access to a virtual reporting dashboard.
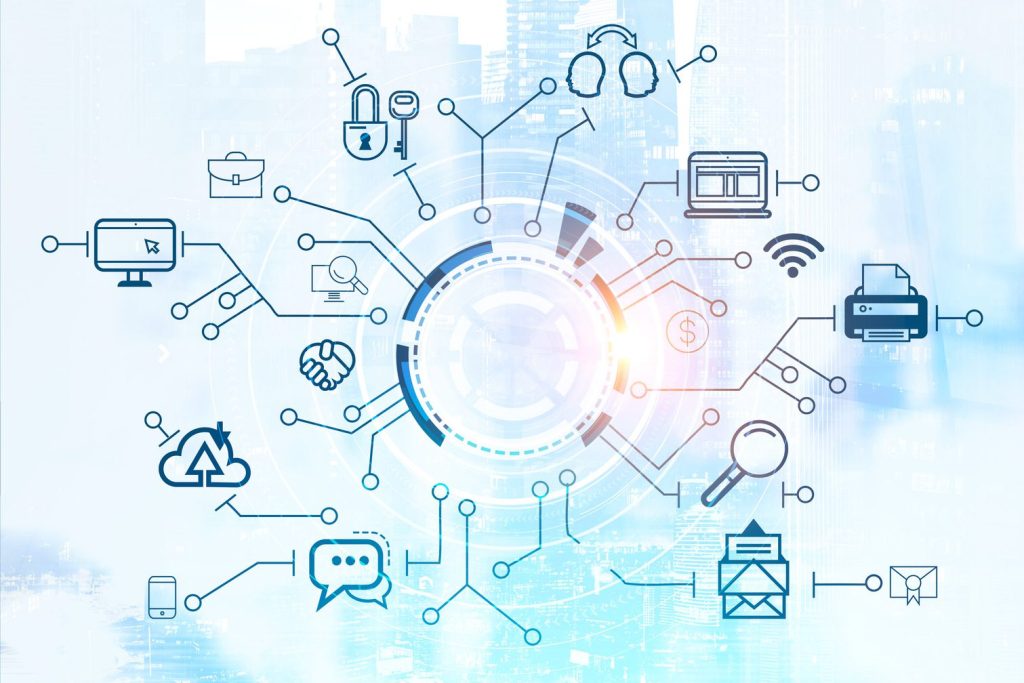
The dashboard provides the user with a real-time data analytics platform that they can use to instantly make adjustments, like adjusting dosages or modifying the whole laundry program, to washer performance without needing to be on-site.
The virtual dashboard can be hosted on a web client, or it can take the form of an app. Through the web client or app interface, the system is able to send out real-time alerts regarding changes in system performance or whether the laundry program needs to be adjusted. It can even inform you as soon if a machine breaks down or becomes out of service.
Despite their similar appearance and operational principles, connected laundry systems offer a host of benefits over traditional laundry systems.
Benefits of a Connected Laundry System
There are many significant benefits to using a connected laundry system.
From streamlined management and easy installation to accurate chemical dosing and increased employee safety, let’s take a look at nine benefits of a connected laundry system:
- Streamlined Management
- Smaller Footprint
- Easy Installation & Preprogramming
- Accurate Chemical Dosing
- Extended Linen Lifespan
- Increased Employee Safety
- Enhanced Employee Productivity
- Reliable Reporting
- Sustainability
1. Streamlined Management
The most significant advantage of a connected laundry system is the streamlined management it offers for your on-premise laundry program.

If an issue occurs with the dispensing system, a technician can make remote adjustments as soon as the problem is identified. This swift response minimizes downtime and enhances overall operational efficiency.
As mentioned before, technicians are also able to notify staff via text or email as soon as they receive a real-time system alert. This proactive communication allows staff to respond promptly, preventing the problem from escalating into a significant, possibly costly, issue.
For example, staff can quickly replace an empty chemical bucket, averting the need for multiple loads to run without detergent, which would otherwise result in higher rewash rates and labor wastage.
2. Smaller Footprint
Connected laundry systems occupy significantly less wall space compared to their traditional counterparts. A single panel, about 3×3 feet in size, can service anywhere upward of ten different washing machines at a time, depending on the model.
This significantly reduces the physical footprint, as conventional dispensing systems require one 3×3 foot panel per washing machine.
3. Easy Installation & Peoprogramming
Efficient preprogramming stands out as a key benefit of connected laundry systems. The ability to preconfigure smart laundry dispensers remotely before on-site installation ensures a quick and hassle-free setup.
Moreover, the technician can manage and fine-tune the connected laundry system from virtually anywhere via an internet connection.
4. Accurate Chemical Dosing
Connected laundry systems shift the responsibility of accurate chemical dosing from humans to smart laundry dispensers, guaranteeing accurate chemical dosing with each wash.
By removing the possibility of human error, you can have confidence that your laundry will consistently receive a thorough and precise cleaning, ultimately reducing the need for rewash cycles and putting an end to the wasteful use of excessive detergent.
Additionally, accurate chemical dosing leads to reduced overall costs, increased worker productivity, and an enhanced geist experience that will result in return visits!
5. Extended Linen Lifespan

Another substantial advantage is the increased lifespan of your linens. The accurate chemical dosing means that your linens are receiving the exact right amount of detergent.
When too much detergent is used, it leaves a buildup of detergent residue on the linens. This transforms previously soft linens into crunchy, scratchy, uncomfortable-to-wear linens, damaging the fabric fibers and causing premature wear outs.
6. Increased Employee Safety
The introduction of automated systems in the chemical dilution process has significantly improved workplace safety for businesses. With the removal of manual dosing, the risk of skin or eye irritation due to contact with harsh chemicals is greatly minimized.
This shift away from hands-on processes means employees no longer have to handle potentially hazardous chemical mixtures, reducing health concerns related to such exposures.
7. Enhanced Employee Productivity
With a connected laundry system handling the chemical dispensing process, employees are freed from the manual, time-consuming task of dosing chemicals for each laundry load.
This automation not only reduces the physical workload but also allows employees to redirect their focus towards more value-added tasks, improving overall operational efficiency.
Additionally, the virtual dashboard allows employees to monitor and manage laundry machines remotely. This capability means that staff members can address any issues promptly, even when off-site, minimizing downtime.
8. Reliable Reporting
The virtual dashboard serves as a centralized hub for comprehensive data analytics, offering detailed reports on machine performance, chemical usage, and overall efficiency. These reports enable data-driven decision-making, allowing your facility to identify patterns, optimize processes, and make informed adjustments.
The real-time monitoring capabilities provided by the virtual dashboard ensures that issues are promptly detected and addressed. Technicians and managers can receive instant alerts via text or email, allowing for swift intervention to prevent potential disruptions.
9. Sustainability
One of the core use cases for a connected laundry system is to optimize wash cycle efficiency. As wash cycle efficiency is optimized over time, less water and electricity are required to achieve the same great cleaning results.
Additionally, you will be using and discarding far less plastic waste by using ready-to-use cleaner rather than detergent that comes in single-use packaging.
Final Thoughts
If you’re seeking to improve the performance and productivity of your commercial laundry equipment, adopting a connected laundry system is the solution you’ve been looking for.
Looking back at the benefits we covered, it’s evident a connected laundry system is key to minimizing operational setbacks, maximizing efficiency, and optimizing overall productivity in your laundry operations
Real-time alerts empower staff to address issues promptly, minimizing downtime and potential disruptions. The precision of chemical dosing through smart laundry dispensers eliminates guesswork, reducing rewash cycles, improving worker safety, and optimizing detergent use for cost savings.
The virtual dashboard’s reporting tools provide valuable insights into operational performance, allowing for proactive adjustments and data-driven decision-making.
This comprehensive approach enables a more efficient and employee-friendly work environment. By leveraging alerts, precise dispensing, and data analytics, your facility can enhance labor productivity while ensuring consistent, high-quality laundry results.
For expert guidance and to learn more about smart laundry solutions, don’t hesitate to reach out to an Imperial Dade facility near you.
Our laundry experts are committed to improving the efficiency and effectiveness of your commercial laundry equipment. Contact us today to set up a consultation with our knowledgeable team and take your laundry operations to the next level with Imperial Dade.