It’s no surprise that dish machines are a key component of any commercial kitchen. These machines clean and sanitize dishes in a timely manner, ensuring proper hygiene and efficient service.
Malfunctioning or out-of-service machines can lead to a host of issues ranging from spotty glasses and dirty dishes to kitchen flooding.
So, what do you do if your commercial dishwasher starts having issues?
When faced with performance-compromising issues, troubleshooting becomes an essential skill. Many times, the issue can be fixed by you and your staff before calling a service technician, saving you time and money.
In this comprehensive guide, we will delve into four of the most common issues that plague commercial dishwashers and provide in-depth insights and practical solutions to resolve them.
4 Most Common Dish Machine Issues
Here are the four most common dish machine issues that we’ve seen in commercial settings.
- Dishes Covered in Food Debris After Washing
- Residue on Dishes and Glasses
- Leaking Dishwashers
- Improper Drainage
Let’s dive right in.
1. Dishes Covered in Food Debris After Washing
Many restaurant kitchen operators find it frustrating when dishes come out of the dishwasher covered in bits of food debris. It results in the dishes needing to be rewashed, which leads to increased labor, utility costs, and wasted product.

Understanding the root causes behind this issue will help us determine how to resolve it. The 3 most common causes of dirty dishes after a wash cycle include:
- Failure to Scrape and Pre-Rinse
- Failure to Regularly Clean and Remove Blockages From Machine Parts
- Overloading
Failure to Scrape and Pre-Rinse
The number one reason why you’re experiencing excess food debris on your dishes is because of a failure to scrape and pre-rinse.
The scrape and pre-rinse step is an often skipped process that plays a pivotal role in the dish-loading process. This step involves rinsing dishes and scraping off food debris before placing them in the commercial dishwasher.
Neglecting this crucial step not only makes it challenging for the machine to clean but also contributes to the accumulation of food debris within the machine, causing blockages.
The Solution
Make sure that your dishwashers scrape and pre-rinse each dish before loading them into the dishwasher.
Failure to Regularly Clean and Remove Blockages From Machine Parts
If a failure to scrape and pre-rinse is not the issue, blockages to the spray arms or strain screen could be what’s hindering the proper cleaning of dishes.
This is often caused by a failure to regularly clean the dish machine spray arms, filters, and screens.
Loose food debris builds up and can easily clog these essential components, impeding their functionality and disrupting drainage. When this happens, it results in good debris being deposited on dishes.
The Solution
Regular cleaning and maintenance of these components are necessary to prevent blockages.
Regular cleaning should include draining and cleaning the water tank, as well as cleaning the wash arms, rinse arms, and pump screen after each meal shift. It should also mean that the dishwasher is left propped open to dry out overnight.
To learn more about regular cleaning and maintenance, check out our guide on How to Clean a Commercial Dishwasher: 3 Expert Tips.
Overloading
If you’ve ruled out the previous two causes and dishes still come out covered in food debris, then chances are overloading is at fault.
While overloading the commercial dishwasher might seem like a time-saving strategy, it often leads to a phenomenon known as “shielding.” This occurs when one dish blocks the spray jets, preventing proper cleaning of dishes behind it.
The Solution
Adhering to proper loading guidelines and avoiding overloading is crucial in resolving this issue.
Dishes should always be stacked with space between each one, so they’re not on top of eachother on the dish rack. Place glasses, cups, bowls, pots and anything that might fill with water during the wash cycle upside down. Lastly, plates and other flat dishes should always be stood up edgewise.
If the problem isn’t a failure to scrape and pre-rinse, blockages in the spray arms and strain screen, or overloading, then you should call a technician to come diagnose and fix the issue.
2. Residue on Dishes and Wares
The appearance of residue on dishes and wares, commonly referred to as water spots, on or around dishes is a common issue. Hard water is the most likely culprit for spotty wares.
Hard Water
Water spots most often occur when water from the commercial dishwasher stays on the dishes for too long, a prevalent issue in hard water areas.
The Solution
Use of a rinse aid; a specialized detergent additive that breaks the tension of the water, allowing it to slide off dishes. Integrating a rinse aid into the dishwashing process can effectively eliminate this problem.
If you’re still experiencing residue on dishes after integrating a rinse aid, call a technician to diagnose and fix the issue.
3. Leaking Dishwasher
A leaking dishwasher not only disrupts the operational flow of a commercial kitchen but can also lead to more extensive damage if left unattended.
There are commonly three root causes of a leaking dishwasher, and they are:
- Damaged Door or Door Gasket
- Damaged Standpipe or Drain Pump
- Stuck Float Switch
Damaged Door or Door Gasket
If you experience a leaky dishwasher, it’s likely that there’s damage to the door or door gasket.
Over time, wear and tear or physical damage can compromise the door’s seal, leading to leaks.
The Solution
Thoroughly inspect the door and gasket for any signs of damage, such as cracks or tears.
If identified, get in touch with a technician to either repair or replace the damaged parts. Otherwise, regular checks and timely replacements can significantly extend the lifespan of these components and prevent water leakage issues.
Damaged Standpipe or Drain Pump
If the door appears to be in good condition, the next most likely issue is that there is something wrong with the drainage system.
The standpipe and drain pump play a crucial role in the removal of wastewater from the machine. A damaged stand pipe or drain pump can impede the proper flow of water, causing overflows and leaks. Standpipes in particular tend to go bad over time.
The Solution
The solution is to be proactive about periodic maintenance. Routine inspections should include a thorough examination of the standpipe for any signs of damage. Additionally, the drain pump should be checked for similar issues.
If damage is found the parts should be replaced immediately. This proactive approach makes for a smoothly functioning drainage system, preventing leaks and potential water damage.
Stuck Float Switch
Lastly, if the door is undamaged and there’s nothing wrong with the drainage system, a stuck float switch could be at fault.
The float switch is a safety mechanism that regulates the water level in the machine. If this switch becomes stuck in the down position it continuously fills the machine, leading to overflows and leaks. This commonly occurs when the float switch is burdened by excessive or large food debris.
The Solution
Regular cleaning and removal of debris from the float switch are the solution. Keeping this component free of obstructions ensures its smooth operation, preventing drainage issues and subsequent leaks.
If you find that there’s nothing holding the float switch down, it may be time to call a technician to diagnose and fix the issue.
4. Improper Draining
Making certain that a commercial dishwasher drains properly is crucial for its overall efficiency and longevity.
Identifying potential causes of drainage issues and implementing effective solutions will help maintain optimal performance. The two most common causes are:
- Damaged Standpipe or Worn Gasket
- Clogged Drain Screen
Damaged Standpipe or Worn Gasket
The most likely culprit when it comes to improper draining is a damaged standpipe or worn gasket.
A standpipe serves as the drainage mechanism for the majority of commercial dish machines. It consists of a lengthy tube equipped with a gasket that seals the drain. However, these components frequently deteriorate, leading to continuous drainage.
The Solution
Regular maintenance, including periodic checks for damage, will reveal any damage before it’s able to significantly interrupt the flow of water. If you do find damage, the parts will have to be replaced.
Clogged Strain Screen
If drainage issues persist even after addressing the standpipe and gasket, the strain screen is the next point of concern.
The strain screen is designed to catch debris and prevent it from entering the drainage system. Over time, however, it can become clogged, hindering proper water flow.
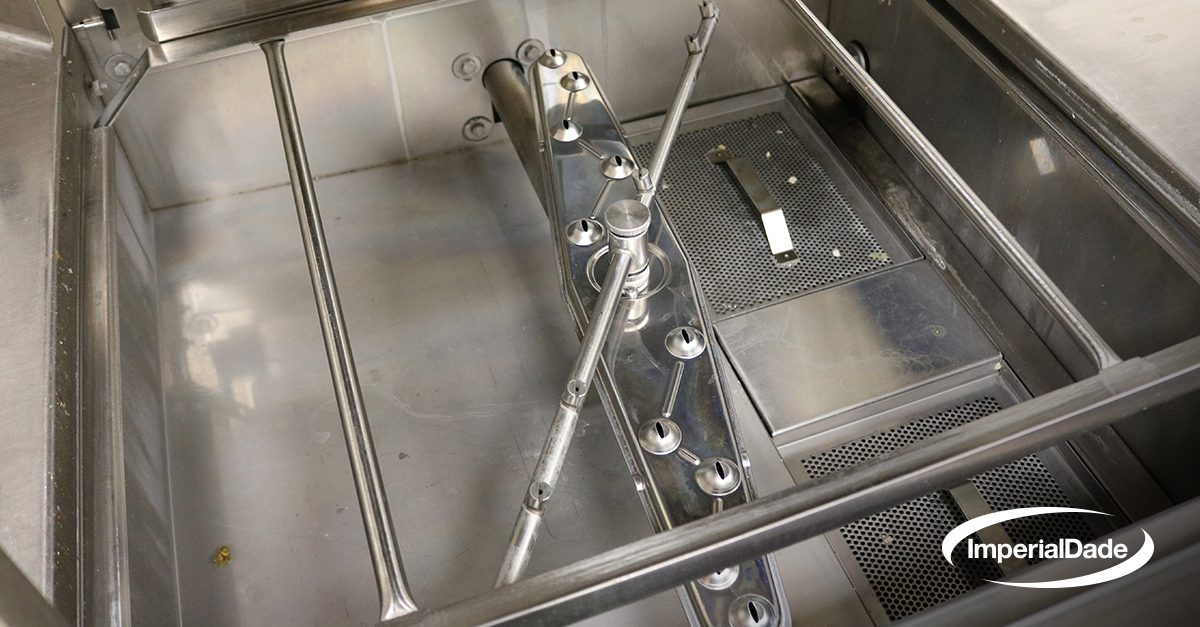
The Solution
The best solution is to regularly clear blockages from the strain screen during scheduled routine maintenance. Doing so should prevent issues related to draining and ensure the longevity of the commercial dishwasher.
If you still experience improper draining after checking the standpipe, gasket, and strain screen, you should call a technician to diagnose and fix the issue.
Final Thoughts
If you want to sustain the efficiency and performance of your commercial dishwasher it’s crucial to adopt a proactive stance regarding the upkeep.
Regular inspections, timely repairs, and preventative measures play a pivotal role in not only resolving common issues but also in enhancing the lifespan of the equipment. This comprehensive approach guarantees consistently spotless and clean dishes in a commercial kitchen setting.
If your preventative maintenance plan needs to be overhauled, or you’re looking for assistance in establishing a well-rounded preventative maintenance plan, connect with an Imperial Dade facility near you.
Our team of highly-trained equipment specialists have decades of knowledge and experience under their belt. Leveraging their specialized expertise, Imperial Dade can offer valuable insights and guidance in optimizing both the functionality of commercial dishwashers and the efficacy of your maintenance program.
This strategic collaboration can lead to improved operational efficiency, reduced downtime, and ultimately contribute to long-term cost savings for your commercial kitchen. Get in touch with one of our equipment specialists today for a free consultation!
Check Out These Related Articles and Videos:
- How to Choose the Right Commercial Dish Machine for Your Business
- Commercial Dishwasher Not Cleaning Dishes? Here’s the fix!
- #1 Reason Your Commercial Dish Machine Isn’t Working Properly
- How to Clean a Commercial Dishwasher: 3 Expert Tips
- How to Properly Load a Dish Machine to Increase Efficiency
- How To Manually Delime a Dish Machine
- 5 Most Common Mistakes in Your Warewashing Program & How to Fix Them