When equipment breaks, it leads to equipment downtime. Without janitorial cleaning equipment, your janitorial cleaning team will have to spend more time completing each task, leading lower worker productivity and higher labor costs.
Knowing the problem affecting your commercial floor buffer can help you better understand whether your buffer requires professional repair or if it is a simple fix.
Some of the most common causes of broken equipment can be fixed by you. Not having to bring your buffer in for service for something that could have been easily fixed will save you time and money, and allow your cleaning team to get back on track faster.
Read on to learn more about the 4 most common problems with commercial floor buffers:
- Floor Buffer Not Turning On
- Floor Buffer Won’t Stay On
- Floor Buffer is Vibrating More Than Normal
- Floor Buffer is Dulling and Scratching the Floor
Problem 1: Floor Buffer Not Turning On
Possible Cause: Not Plugged In
If your floor buffer will not turn on, check to see that the buffer is plugged into the wall outlet. The plug may have fallen out or have been placed in a faulty outlet.
The Fix: Double-check that the issue is not originating from the wall outlet rather than the floor buffer. Test the outlet by plugging in a second device to check for power. If the second device does not receive power, the wall outlet is not working. If the second device does receive power, the problem is not with the wall outlet.
Possible Cause: Damaged Or Frayed Power Cords
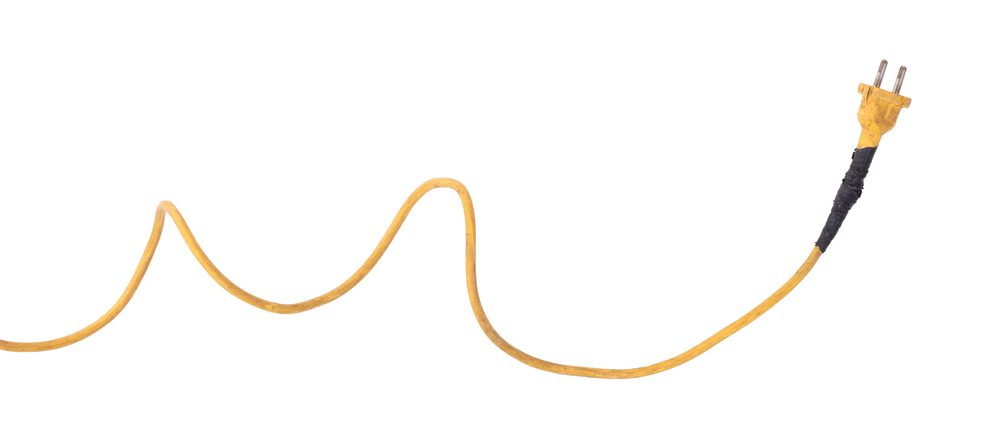
Damaged or frayed power cords may be preventing the machine from getting any power.
Power cords are commonly damaged from improper storage and use.
Cords should be stored according to the manufacturer’s specifications. Most machines will have a cord hook to wrap the cord around. Do not leave the cord unwrapped in storage.
When in use, the operator must carefully maneuver around cords so that the buffer does not run over the cord. Cords which are run over become damaged and pose a safety risk to the user. To avoid running over the cord, the operator should start the machine closest to the outlet they are using as a power source and then work away from the plug.
Ripping the power cord from the outlet will cause the prongs to become bent and can cause the plug to separate from the cord. Your cord should have 3 prongs.
The Fix: Check the power cord for bent prongs, missing prongs, or frayed areas. If there is damage to the protective covering of the cord or prongs, the power cord will need to be replaced. The cord should be replaced by a certified technician.
Machine service and maintenance should only be performed by a certified technician.
Problem 2: My Floor Buffer Won’t Stay On
Possible Cause: Floor Buffer Trips Wall Circuit
A tripped wall circuit breaker is caused by a temporary overload on the circuit or a short in the device plugged into the electrical outlet.
Circuits trip when too much power is being drawn or too much strain is put on the circuit. If the motor draws high amperage, the electrical circuit breaker will stop providing power.
The Fix: Test to see if the outlet will provide power to another device. If there is power to the second device, the problem is not with the outlet. The buffer circuit breaker may have tripped.
Possible Cause: Floor Buffer Trips Machine Circuit
A circuit breaker on the machine is used to protect the motor on the buffer.
The most common reason the buffer circuit trips is that some of the floor buffer’s cord is still wrapped around the cord hook. You should never operate the floor buffer with the cord still wrapped around the cord hook. When wrapped around the cord hook, the cord will not receive enough power and will cause strain on the machine, ultimately tripping the buffer circuit.
The Fix: If the cord is still wrapped around the cord hook, release the cord and reset the buffer circuit breaker.
The more a floor buffer’s circuit trips, the weaker the circuit will become, causing it to trip more frequently.
Pro Tip: If you are not sure if the electrical circuit or the buffer circuit has tripped, start by checking the wall circuit. Plug a second device into the electrical outlet to see if it will provide power to the second device. If the second device does not power on, reset the electrical outlet. If the wall outlet does power the device, check the machine circuit breaker.
Problem 3: Floor Buffer Is Vibrating More Than Normal
Possible Cause: Floor Pad Is Installed Incorrectly

The floor pad must be centered on the machine. If the pad is not centered on the pad driver, it will not be balanced and will cause the machine to shake or vibrate on the floor.
The Fix: Removing and reinstalling the pad should fix the problem.
Possible Cause: Floor Pad Is Damaged Or Worn
A damaged or worn floor pad will not sit evenly on the floor and can cause the pad driver to wobble while it is rotating.
The Fix: Removing and replacing the floor pad should solve the problem.
Possible Cause: Motor Issues
If the problem is not with the floor pad, the issue probably lies within the motor.
The Fix: Motor related issues are typically more difficult to fix. Consult an authorized service technician.
Machine service and maintenance should only be performed by a certified technician.
Pro Tip: Buffers that come with warranty may require that machine maintenance and service only be performed by certified technicians or the warranty will be voided. Check with your manufacturer before performing any service or maintenance to your buffer.
Problem 4: Floor Buffer Is Dulling Or Leaving Scratches On The Floor
If your floor buffer is dulling or scratching the floor, your floor buffer is probably not broken.
Possible Cause: Wrong Floor Pad
When selecting a floor pad for a buffer, you will want to choose the least aggressive pad for the floor finish that will best perform the maintenance procedure. Typically, the darker the floor pad, the more aggressive or abrasive the pad is. The more aggressive the face of a pad, the more finish it will remove. Using a pad that is too aggressive for your finish will cause streaks and scratches to your floor.
The Fix: To make sure you are using the right floor pad for the cleaning procedure and floor finish, check out our article and video: What Is The Best Floor Pad For Your Buffer Or Burnisher? [Video]
Final Thoughts
Floor buffers are an important part of your hard floor care program and when your floor buffer isn’t working properly, it is costing you time and money.
Many times the cause of your floor buffers problem can be solved by you, but if it is a more complex problem, Imperial Dade locations have the training to help keep your equipment operating in peak condition.
Our trained technicians can prevent surprise breakdowns and make sure your equipment is functioning as it should. If you’re located in the United States, Puerto Rico, or the Caribbean, we can provide you with top-rated service for your equipment.
Visit our site to learn more about our equipment service and repair program or to schedule a consultation today.
Some other articles about floor buffers you might be interested in include: