Any business with a commercial pressure washer knows by now that it can be a powerful addition to its fleet of cleaning equipment. These machines swiftly remove dirt, grime, and stains, restoring surfaces to pristine condition with efficiency and effectiveness.
A malfunctioning or broken commercial pressure washer can be due to a range of problems, from low pressure to overheating.
So, what steps should you take when pressure washer issues arise?
When confronted with operational challenges, pressure washer troubleshooting becomes an essential skill. Oftentimes, the problem can be solved by you and your staff before calling a service technician, saving you time and money.
This comprehensive guide will delve into five of the most common issues encountered with commercial pressure washers, offering detailed insights and practical solutions to address them effectively.
5 Common Commercial Pressure Washer Issues
Our experts compiled this list of five of the most common pressure washer issues that they encounter in the field:
- Pressure Washer Has Water Low Pressure
- Pressure Washer Leaking Water From the Bottom
- Pressure Washer Pump Issues
- Pressure Washer Engine Problems
- Pressure Washer Overheating
Now, let’s take a look at how to troubleshoot each one!
1. Pressure Washer Has Low Water Pressure
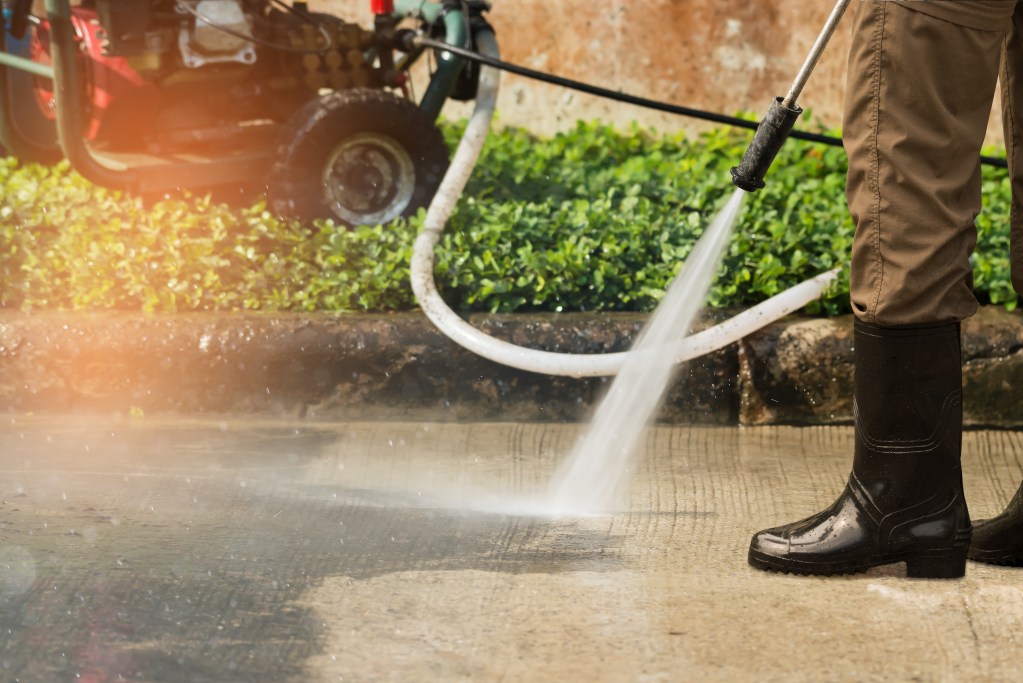
The main purpose of a commercial pressure washer is to deliver a high-pressure stream of water. If your pressure washer has low water pressure, it can be impossible to complete the cleaning tasks that you purchased it to handle.
The only way to solve this issue is to understand what caused it. When your pressure washer has low pressure, there are a handful of causes you should investigate.
- Clogged Nozzle
- Clogged Water Inlet Filter
- Blocked or Damaged Hose
- Worn-Out Pump
Clogged Nozzle
The most likely culprit is a clogged nozzle. It’s common for dirt or debris to accumulate in the nozzle over time, causing a clog that restricts or inhibits water flow.
The Solution
The solution is to clean or replace the nozzle.
You can clean the nozzle by soaking it in white vinegar overnight. The following morning, run the nozzle under a faucet and any remaining debris should flush out. You can easily avoid clogs by regularly cleaning the nozzle.
If you’re unable to remove the obstruction, you may need to replace the nozzle altogether.
If you’re sure the nozzle isn’t clogged, then the next step is to check for a clogged water inlet filter
Clogged Water Inlet Filter
The water inlet filter is a fine-screen mesh that blocks dirt and other debris from entering the commercial pressure washer. This will collect enough dirt over time that it can affect the commercial pressure washer’s water pressure output.
The Solution
The solution is to check the water inlet filter for clogs. If you find one, clean it out by running the inlet under a tap.
If your pressure washer has low pressure after doing this, it could be an issue with the hose.
Blocked or Damaged Hose
A blocked or damaged hose can greatly impede water flow to the commercial pressure washer.
The Solution
First, check to see if there is a kink in the hose. Kinks are common and form over time, making this the most likely reason your pressure washer has low pressure. If there aren’t any kinks, look for a blockage.
One way to check for blockages is by attaching one end of the hose to a water supply and running it. If water comes out of the other end unobstructed, you know there are no blockages. If water is not coming out the other end, there is a blockage. Massage the hose to work the blockage out.
After clearing the hose of any kinks or blockages, inspect it for tears and leaks. Tears and leaks occur over time due to natural wear. If you find any, you must replace the hose with a new one.
If the hose checks out, the dip in water pressure could be due to a worn-out pump.
Worn-Out Pump
The pump can lose efficiency and even fail over time as it goes through the motions of regular wear and tear. When this happens, water pressure is greatly affected.
The Solution
Inspect the pump. If it shows signs of wear or damage, it’ll need to be repaired or replaced.
If, after checking the pump, water pressure issues persist, you’ll have to call a technician to diagnose and fix it.
2. Pressure Washer Leaking Water From the Bottom
If your pressure washer is leaking, that’s a sure sign that something is wrong. It can lead to a pool of water forming around the commercial pressure washer, leaving water spots, and creating unsafe working conditions.
To fix your leaky pressure washer, you must get to the root of the issue. Here are three potential causes for water leaks:
- Damaged Hose
- Faulty Seals or O-rings
- Loose Connections
Damaged Hose
Hoses are prone to damage from wear and tear, sharp objects, and improper storage. Any of these factors can result in a leak.
The Solution
Meticulously inspect the hose for cuts or damage, and replace it if needed.
If the hose appears to be in good condition, and you don’t notice it leaking, then the next thing you should check is for faulty seals or O-rings.
Faulty Seals or O-Rings
The seals and O-rings on a pressure washer are there to help prevent leaks from happening. However, these can deteriorate over time, causing water to escape.
The Solution
Just as with the hose, meticulously inspect the seals and O-rings for signs of wear, replacing them where necessary.
If none of the seals and O-rings are deteriorated, the next most likely culprit is that there’s a loose connection somewhere within the commercial pressure washer.
Loose Connections
A commercial pressure washer is made up of many complex parts, including the hose, trigger sprayer, spray wand, and nozzle.
Each of these parts has connections that need to be tightly secured for the commercial pressure washer to operate properly. Any loose connections can result in water leaks.
The Solution
The solution is to check that all connections between each of the aforementioned parts are tightly secured.
If, after checking to make sure that everything is tightly connected, your pressure washer has low pressure, you’ll have to call in a technician to diagnose and fix the problem.
3. Pressure Washer Pump Issues
The pump plays a very important role in a pressure washer. It uses a motor or engine to take water from the water supply and help turn it into a concentrated, high-pressure stream of water. When the pump isn’t working properly, the commercial pressure washer is incapable of performing at its best.
When the pump isn’t performing as expected, there are three main causes:
- Lack of Water Supply
- Air in the Pump
- Worn-Out Pump
Lack of Water Supply
An inadequate water flow doesn’t just hinder the pump’s performance; it can damage it.
The Solution
The solution here is simple; make sure that there is always a sufficient and uninterrupted water supply to the pressure washer. This can mean ensuring that the spigot you’re connected to remains open or that the hose connecting the water supply to the pump doesn’t have a kink or blockage.
If you’re positive that a steady water supply isn’t the issue, air in the pump may be causing the problem.
Air in the Pump
Air pockets can reduce pump efficiency, causing a host of problems like loss of pressure, inconsistent spray patterns, and accelerated wear and tear.
This is a serious issue that should be addressed promptly if you believe it’s causing an issue with your pump.
The Solution
Thankfully, the solution here is an easy one. All you need to do is purge air from the pump.
You can do this by running water through the pump before starting the motor or engine. After doing this, if pump issues persist, take a look at the pump itself to check the condition it’s in.
Worn-Out Pump
As we went over earlier, pumps are prone to wearing out over time as a result of regular wear and tear.
Check the pump for signs of wear. If it’s worn out, you’ll have to have the pump repaired or replaced. If the pump is in good condition, then the best course of action is to call in a technician to diagnose and fix the problem.
4. Pressure Washer Engine Problems
Gasoline-powered pressure washers are more robust than electric-powered models, offering increased durability and cleaning capabilities. The tradeoff, however, is that these machines need to be more complex and require more moving parts. As a result, they can experience more engine-maintenance issues than an electric-powered model.
When you experience pressure washer engine problems on a gas, there are three common causes to investigate.
- Dirty Carburetor
- Using Old Fuel
- Faulty Spark Plug
Dirty Carburetor
Most of the time, pressure washer engine problems stem from a dirty carburetor. Carburetors can become dirty over time as debris and contaminants are introduced during normal use. Another way carburetors can become dirty is if there are contaminants in the fuel.
The Solution
The solution is to have the carburetor cleaned out. Cleaning a carburetor is a very involved process that will likely require the help of a trained technician.
To avoid running into a dirty carburetor in the future, change the fuel filter regularly.
If the carburetor is clean and you still experience engine problems, the next most likely reason is that you’re using old fuel.
Using Old Fuel
Gasoline degrades over time. When it does, it’s considered “stale gas.” Stale gasoline loses a significant portion of its combustibility, which has a direct effect on engine performance.
The Solution
The solution is to replace your gasoline supply with fresh gasoline.
When stored properly, gasoline starts to degrade in three-to-six months. Ideally, you should use clean fuel each time you use your commercial pressure washer. If the machine is not used regularly, use a gasoline stabilizer to keep the gasoline fresh.
If you use fresh gasoline and you’re still experiencing engine problems, take a look at the spark plugs.
Faulty Spark Plugs
Spark plugs are what supply the “spark” that ignites the pressure washer’s engine on gas machines. Faulty spark plugs can lead to ignition problems that affect engine performance.
The Solution
The solution here is to check the spark plugs on your commercial pressure washer and make sure that there are no signs of wear or damage. If there are, you’ll have to replace them.
If the carburetor is clean, you use fresh gasoline, and the spark plugs are in good condition, you’ll have to have a technician come diagnose and fix the issue.
5. Pressure Washer Overheating
Pressure washers can overheat. It is a problem that needs to be taken very seriously. Overheating causes damage to various internal components of the pressure washer. In a best-case scenario, multiple components are severely damaged and require costly repairs. In a worst case scenario, the pressure washer will need to be replaced.
Let’s take a look at each of the most likely causes behind pressure washer overheating.
- Continuous Use Without Breaks
- Malfunctioning Thermal Relief Valve
Continuous Use Without Breaks
The main reason why a pressure washer overheats is because the operator uses it for a long period of time without any breaks. See the owner’s manual for recommendations.
The Solution
The solution is simply to avoid overworking the pressure washer. Make sure that operators know to take breaks and allow the pressure washer to cool down before resuming use.
If you’re sure the commercial pressure washer hasn’t been overworked but it’s still overheating, then the issue is likely rooted in a malfunctioning thermal relief valve.
Malfunctioning Thermal Relief Valve
The main function of a thermal relief valve is to prevent the pump from overheating by circulating cool water. When this malfunctions, it leads directly to overheating. The telltale sign of a malfunctioning thermal relief valve is when the commercial pressure washer constantly discharges water onto the ground or if the valve doesn’t close properly.
The Solution
The solution is to check and see if the valve is closed properly. If the valve is tightly secured and water is still continuously discharged, then you know that there’s a problem with the thermal relief valve.
Replace the thermal relief valve and the overheating problem should disappear.
If you still experience overheating after replacing the thermal relief valve call a technician to diagnose and fix the problem.
Final Thoughts
Pressure washer troubleshooting is a critical skill for being able to diagnose and fix issues with your equipment. However, the best way to avoid breakdowns and prolong the useful life of your commercial pressure washer is through a preventative maintenance plan.
Regular inspections, timely repairs, and preventative measures are essential.
Our team of highly-trained equipment specialists have decades of knowledge and experience under their belt. Leveraging their specialized expertise, Imperial Dade can offer valuable insights and guidance in optimizing both the functionality of your pressure washers and the efficacy of your maintenance program.
This strategic collaboration can lead to improved operational efficiency, reduced downtime, and ultimately contribute to long-term cost savings for your fleet of janitorial equipment. Get in touch with one of our equipment specialists today for a free consultation!